Absorption chillers use heat, instead of mechanical energy, to provide cooling. The mechanical vapor compressor is replaced by a thermal compressor (see figure) that consists of an absorber, a generator, a pump, and a throttling device. The refrigerant vapor from the evaporator is absorbed by a solution mixture in the absorber. This solution is then pumped to the generator where the refrigerant is revaporized using a waste steam heat source. The refrigerant-depleted solution is then returned to the absorber via a throttling device. The two most common refrigerant/absorbent mixtures used in absorption chillers are water/lithium bromide and ammonia/water.
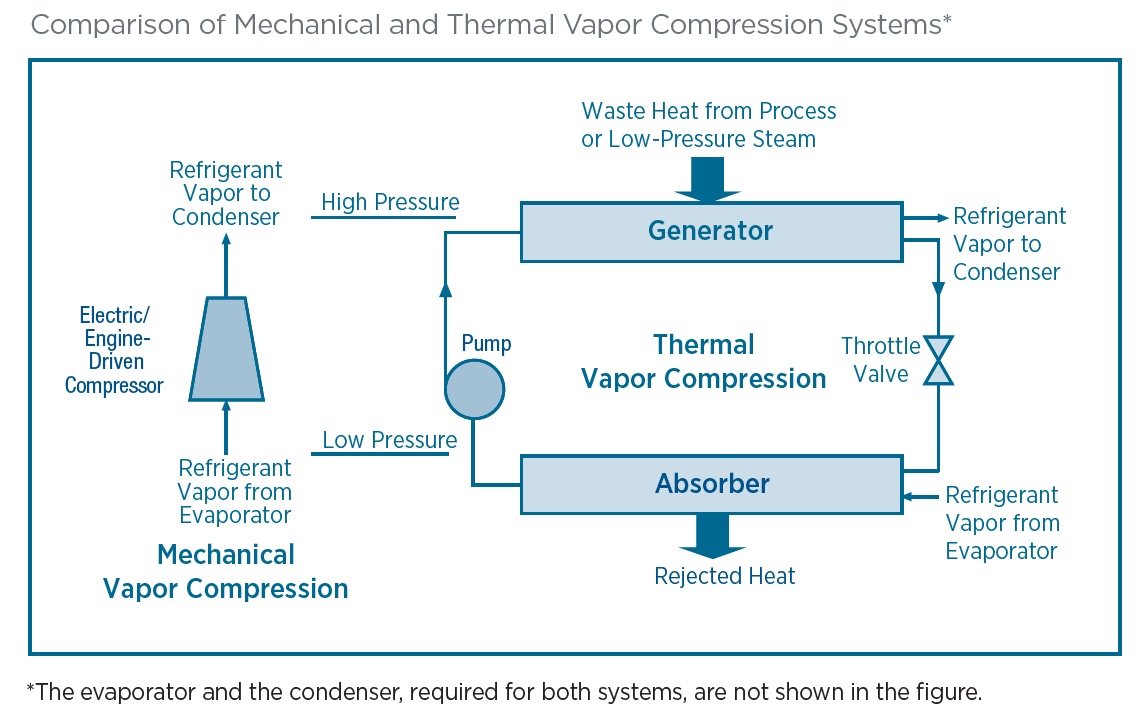
Compared to mechanical chillers, absorption chillers have a low coefficient of performance (COP = chiller load/heat input). Nonetheless, they can substantially reduce operating costs because they are energized by low-grade waste heat, while vapor compression chillers must be motor- or engine-driven.
Low-pressure, steam-driven absorption chillers are available in capacities ranging from 100 to 1,500 tons. Absorption chillers come in two commercially available designs: single-effect and double-effect. Single-effect machines provide a thermal COP of 0.7 and require about 18 pounds of 15-pounds-per-square-inch-gauge (psig) steam per ton-hour of cooling. Double-effect machines are about 40% more efficient, but require a higher grade of thermal input, using about 10 pounds of 100- to 150-psig steam per ton-hour.
Example
In a plant where low-pressure steam is currently being exhausted to the atmosphere, a mechanical chiller with a COP of 4.0 is used 4,000 hours per year (hr/ yr) to produce an average of 300 tons of refrigeration. The cost of electricity at the plant is $0.06 per kilowatt-hour (kWh).
An absorption unit requiring 5,400 pounds per hour of 15-psig steam could replace the mechanical chiller, providing annual electrical cost savings of:
- 300 tons x (12,000 Btu/ton / 4.0) x 4,000 hr/yr
- x $0.06/kWh / 3,413 Btu
- = $63,287 in Annual Savings
This tip is provided by the U.S. Department of Energy – Energy Efficiency and Renewable Energy and originally published by the Industrial Energy Extension Service of Georgia Tech.
For suggested actions and resources, click to download the complete US Department of Energy Tip Sheet.