Every pound of steam saved is a pound that does not have to be produced by the boiler. That’s why recovering flash steam is a great way to reduce energy costs.
Flash steam is steam that is created when condensate at a higher pressure and temperature is released to a lower pressure and the condensate cannot exist as a liquid in the new condition.
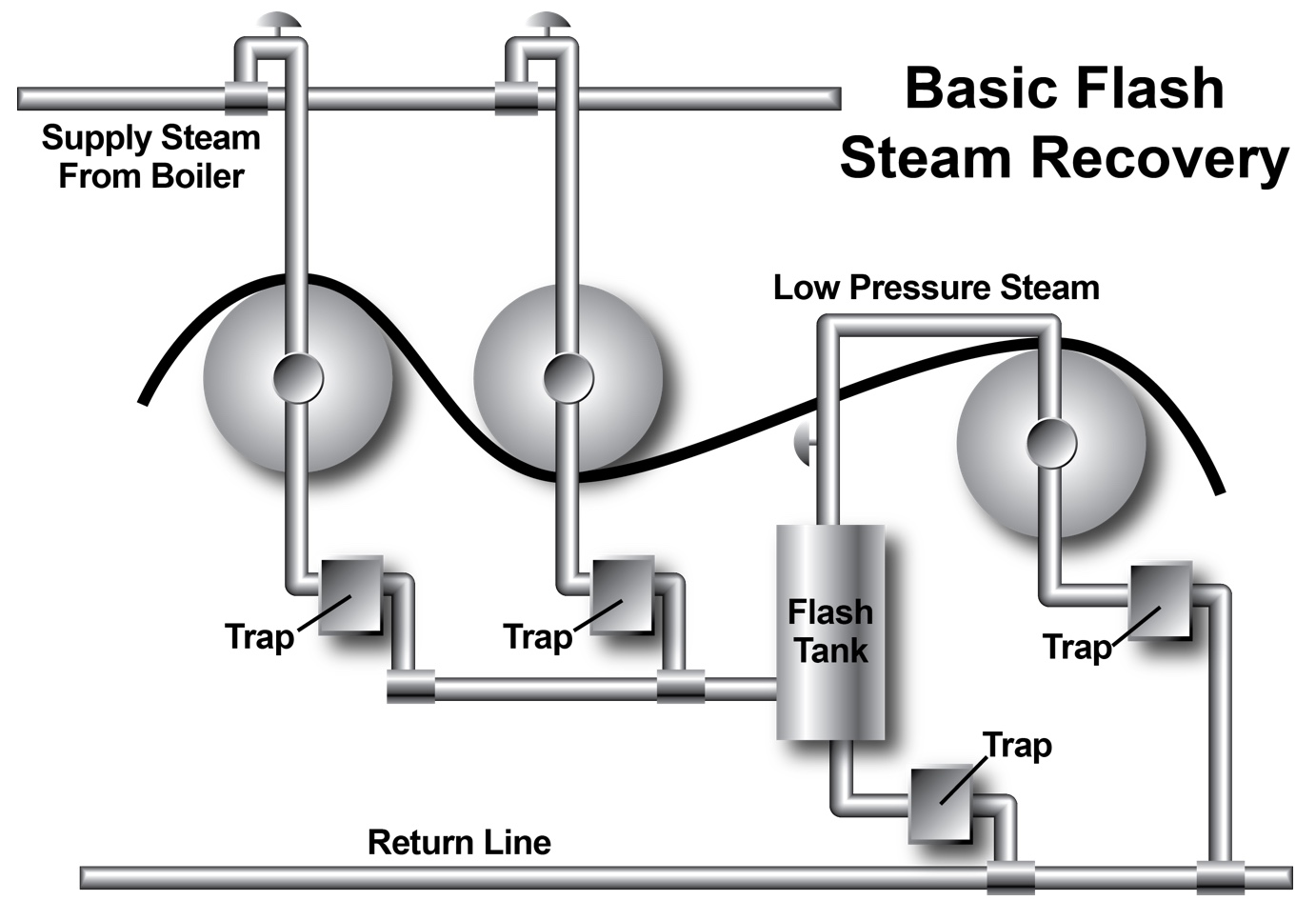
Flash steam can be used for the same purposes as live steam because it has exactly the same latent heat content as boiler steam. If this latent heat is not put to some service, the heat energy that was used to produce it is partially wasted.
So how much of a financial impact can saving flash steam make? Here is an example:
In a plant where the cost of steam is $8.00 per million Btu ($8.00/MMBtu), saturated steam at 150 pounds per-square-inch-gauge (psig) is generated, and a portion of it throttled to supply 30-psig steam. Assuming continuous operation, the annual energy savings of producing low-pressure steam by flashing 5,000 pounds per hour (lb/hr) of 150-psig condensate is $40,924. Over 10 years that’s over $400,000 in savings!
Determine if Flash Steam Recovery is right for your plant
Campbell-Sevey can help you determine the potential for high pressure condensate flashing by completing a plant survey that:
- Identifies all sources of high pressure condensate
- Determines condensate flow and duration, as well as the heat recovery potential due to flashed steam production
- Identifies compatible uses for low-pressure steam
- Estimates the cost effectiveness of installing appropriate heat recovery devices and interconnecting piping
Click here to
download and review Armstrong’s complete Flash High-Pressure Condensate to Regenerate Low-Pressure Steam best practices tip, along with suggested actions.