Consider Installing Turbulators on Two- and Three-Pass Firetube Boilers
Firetube Boilers
The packaged firetube boiler is the most common boiler design used to provide heating or process steam in industrial and heavy commercial applications. The American Boiler Manufacturers Association (ABMA) surveyed sales of high-pressure [15- to 350-pounds-per-square-inch-gauge (psig)] firetube and small watertube boilers between 1978 and 1994. ABMA found that firetube boilers comprised more than 85% of the sales of these boilers to industry.
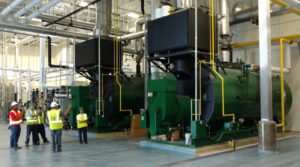
Although firetube boilers are available in ratings up to 85,000 pounds of steam per hour (lb/hr), they are generally specified when the required steam pressure is under 150 psig and the boiler capacity is less than 25,000 lb/hr. Watertube boilers are designed for larger, high-pressure, and superheated steam applications.
In a firetube boiler, hot combustion gases pass through long, small-diameter tubes, where heat is transferred to water through the tube walls. Firetube boilers are categorized by their number of “passes,” or the number of times that the hot combustion gases travel across the boiler heat-exchange surfaces. For example, a two-pass boiler provides two opportunities for hot gases to transfer heat to the boiler water. Hot combustion gases enter the tubes in a turbulent flow regime, but within a few feet, laminar flow begins and a boundary layer of cooler gas forms along the tube walls. This layer serves as a barrier, retarding heat transfer.
Turbulators, which consist of small baffles, angular metal strips, spiral blades, or coiled wire, are inserted into the boiler tubes to break up the laminar boundary layer. This increases the turbulence of the hot combustion gases and the convective heat transfer to the tube surface. The result is improved boiler efficiency. Turbulators are usually installed on the last boiler pass.
Turbulator installers can also balance gas flow through the tubes by placing longer turbulators in the uppermost tubes. This practice increases the effectiveness of the available heat-transfer surface by eliminating thermal stratification and balancing the gas flow through the firetubes.
Applications
Turbulators can be a cost-effective way to reduce the stack temperature and increase the fuel-to-steam efficiency of single-pass horizontal return tubular (HRT) brick-set boilers and older two- and three-pass oil- and natural-gas-fueled firetube boilers. Turbulators are not recommended for four-pass boilers or coal-fired units. A four-pass unit provides four opportunities for heat transfer. It has more heat exchange surface area, a lower stack temperature, higher fuel-to-steam efficiency, and lower annual fuel costs than a two- or three-pass boiler operating under identical conditions. New firetube boilers perform better than older two- and three-pass designs.
Turbulators can also be installed to compensate for efficiency losses when a four-pass boiler is being converted to a two-pass boiler because of door warpage and loose and leaking tubes.
Turbulators are substitutes for more costly economizers or air-preheaters. They are simple, easy to install, and low cost. Their installed cost is about $10 to $15 per boiler tube. Current turbulator designs do not cause a significant increase in pressure drop or contribute to soot formation in natural-gas-fired boilers. Turbulators are held in place with a spring lock and are easily removed to allow for tube brushing.
Turbulators come in various lengths and widths and should be installed by a qualified installer. To avoid combustion problems, the boiler burner should be retuned after the turbulators have been installed. The installer must also verify that the stack temperature does not fall below the flue gas dew point.
Price and Performance Example
A manufacturing facility installed 150 turbulators into its firetube boiler. Tests conducted both before and after turbulator installation indicated a reduction in the stack gas temperature of 130°F. More combustion heat was being transferred into the boiler water. Because each 40°F reduction in the boiler flue gas temperature results in a 1% boiler-efficiency improvement, overall boiler efficiency has improved by about 3.25%. Fuel costs have decreased by approximately 4%.
A manufacturing facility installed 150 turbulators into its firetube boiler. Tests conducted both before and after turbulator installation indicated a reduction in the stack gas temperature of 130°F. More combustion heat was being transferred into the boiler water. Because each 40°F reduction in the boiler flue gas temperature results in a 1% boiler-efficiency improvement, overall boiler efficiency has improved by about 3.25%. Fuel costs have decreased by approximately 4%.
Example
Consider a two-pass firetube boiler that consumes 60,000 million Btu (MMBtu) of natural gas annually while producing 15,000 lb/hr of 100-psig saturated steam. What are the annual energy and cost savings, given that the installation of turbulators improves the boiler efficiency from 79% (E1) to 82% (E2)? Natural gas is priced at $8.00/MMBtu.
- Annual Energy Savings = Annual Fuel Consumption (MMBtu) x (1 – E1/E2) or 60,000 MMBtu x (1 – 79/82) = 2,195 MMBtu
- Annual Cost Savings = $8.00/MMBtu x 2,195 MMBtu/yr = $17,560
If the boiler has 250 tubes and the installed cost for the turbulator is $15 per tube, the simple payback on the investment in the energy efficiency measure is:
- Simple Payback = (250 tubes x $15/tube)/$17,560/year = 0.21 year
This tip is provided by the U.S. Department of Energy – Energy Efficiency and Renewable Energy and is adapted from material provided by Brock Turbulators and Fuel Efficiency, LLC, and reviewed by the AMO Steam Technical Subcommittee.
For suggested actions and resources, click to download the complete US Department of Energy Tip Sheet.