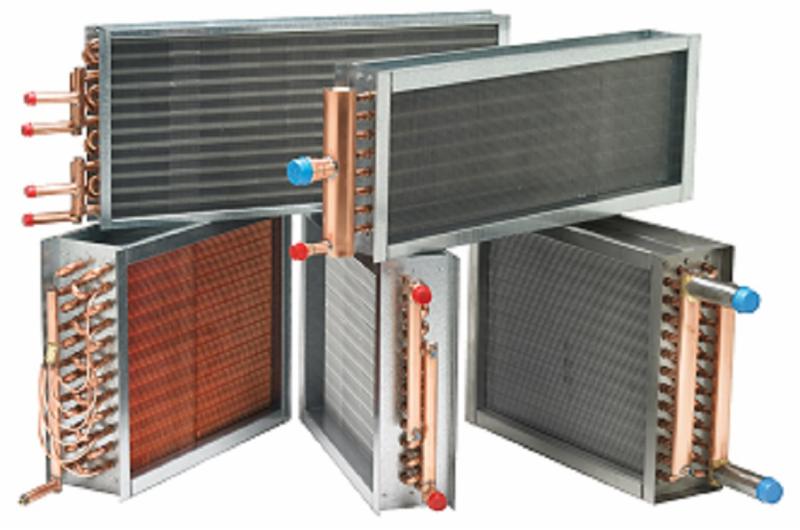
- The maximum height and length of the coil – This is needed to determine which way a coil that is above a ceiling or in-between joists can be expand to keep the air velocity at a reasonable speed.
- Required CFM volume of air
- Entering air temperature and either desired leaving air temperature or desired BTUH load required
- Entering water temperature and either desired leaving water temperature or desired GPM water volume – There’s a lot of difference between a coil selection at 180˚ F entering water and 140˚ F entering water temperature. There’s also a large difference when the leaving water is based on a 20 or 40 degree temperature difference (Example: 180˚ F in and 160˚ F out vs. 180˚ F in and 140˚ F out).
- Required maximum air resistance (inches of water)
- Required maximum water resistance (feet of water)
- Flange or slip and drive type mounting
- Coil construction – This will include fin thickness if you want to wash and clean coils and whether you want brazed copper sweat connections or threaded MPT connections.
- Low water flow – This can happen on many coils under 500 CFM, because the calculated water volume (GPM) is so low that the coil actually develops “laminar flow” – flow of water so low that it destroys heat transfer. This problem can reduce a coil capacity by 75 to 80 percent. Simply use a smaller diameter tube and the water velocity can usually be raised above 1 FPS.
- Air stratification – A coil’s efficiency is based on using the entire effective area of the coil, however unequal air flow can be created when entering air is too close to a fan or a bend in the ductwork. To reduce stratification a baffle or turning vanes may be required so the coil can receive air properly across the effective area.
- Lack of access – Dirty coils reduce heat transfer and increase resistance and operating expenses, yet many hot water coils are mounted in ducts so tightly that there is no access to the fins and tube surface. Simply provide access through a hand hole door to clean the coil at least every 4 to 5 years.
Installing Hot Water Booster Coils